SUSTAINABLE CHEMISTRY CENTER
Polymer Technology RESEARCH GROUP
Area Leader
Piotr Jankowski, PhD Sc. Eng.
phone +48 453 056 197
piotr.jankowski@ichp.lukasiewicz.gov.pl
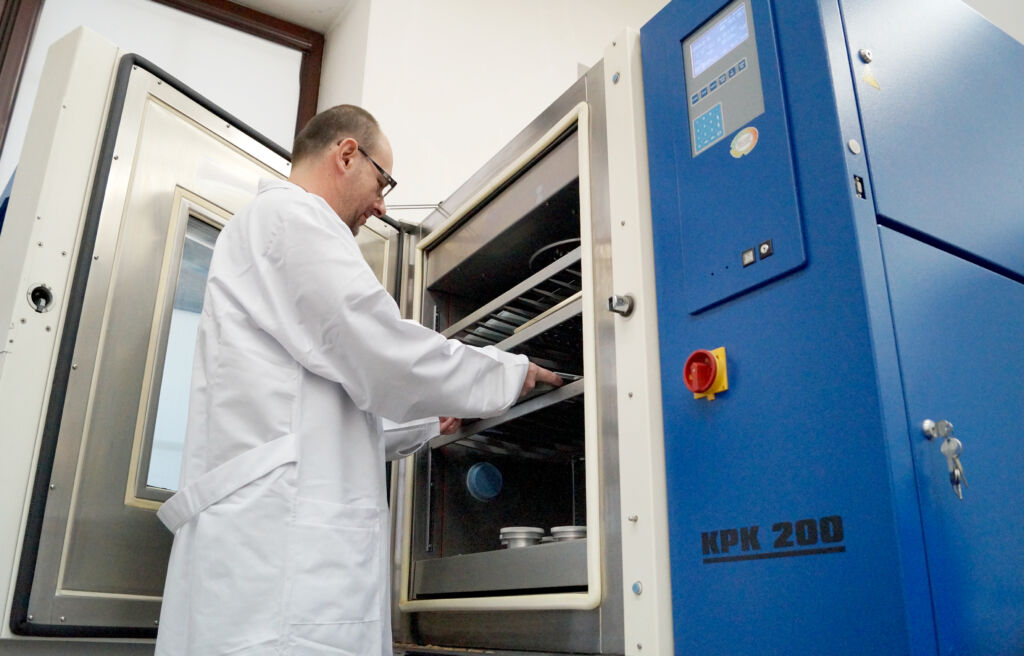
Head
Dr. Regina Jeziórska, Eng.
phone +48 453 056 185
regina.jeziorska@ichp.lukasiewicz.gov.pl
Research topics
- Chemical modification of thermoplastics by reactive extrusion
- Recycling of thermoplastics, including by reactive extrusion
- Filling and reinforcement of thermoplastics
- Biodegradable polymer composites using raw materials of natural origin
- Polymer nanocomposites
- Modification and processing of engineering plastics, including PPO
- Investigations into the properties of polymeric materials
- Manufacturing technology and modification of polymeric materials
Technologies offered
- New generation engineering plastics from recycled materials (PET bottles)
- Thermoplastic elastomers from waste multilayer films
- Wood-based composites from waste multilayer films
- Thermoplastic starch
- Biodegradable polymers containing thermoplastic starch
- Polymer composites with nanosilica
- Polymer composites from polycarbonate waste
Equipment
- Arburg 420M Allrounder 1000-250 injection moulding machine – equipped with Priamus injection process monitoring system and moulds for injection moulding of mechanical test pieces
- Berstorff ZE-25-33D twin-screw co-rotating roller extruder – equipped with K-Tron mass dosing unit
- KraussMaffei Berstorff ZE25Ax51D-UTXi-UG twin-screw co-rotating extruder – equipped with bulk metering set; L/D 51
- Twin-screw co-rotating extruder, ThermoHaake PTW 16/25
- Sthepan UMC 12 mixers
- Collin’s P 300 E laboratory plate press – equipped with a rapid cooling system for the press plates to increase productivity
- Cutting mill, SM100, Retsch – collection vessel capacity: 5 l, sieves: mesh size 0.25; 0.75; 1.5; 4; 8; 10; 20 mm
- Montan MD 11C and Somos TF 10 molecular sieve dryers
- Two-wheeler, Schwabenthan Berlin
- Mytron climate chamber KPK 120
- Thermowell TGA/SDTA 851e, Mettler Toledo. Temperature range 25-1000°C, max. sample volume 900 µl, max. sample weight 5 g
- DSC differential calorimeter, Temperature range 30-400°C
- Apparat for the TotalPerm gas vapour permeability test by ExtraSolution
- RDS II Dynamic Respectrometer, Rheometrics Measurement at temperatures from -160°C to 500°C
- Plastometer (Ceast, Italy type ModularMelt Flow) Control with 0.1°C in the range 100-400°C; piston load up to 21.6 Kg
- Vicata/HDT CEAST HV3 softening temperature apparatus, measuring at temperatures up to 300°C
- Instron 5500R Testing machine for tensile and flexural testing of materials, equipped with 2 testing heads: up to 0.5 kN, 5 kN, 100 kN.
- Shore hardness tester – hardness measurement scale a I d
- Hardness tester – hardness measurement by the press-in ball method
- Zwick impact hammer – measuring range up to 4 J
- Laboratory reactors and autoclaves
Research methodology
- Evaluation of static tensile and flexural properties – Standards EN ISO 527-2 and EN ISO 178
- Charpy impact tests with and without notching according to EN ISO 179-1
- Impact tests according to Izod EN ISO 180
- Heat deflection temperature (HDT) according to EN ISO 75-1
- Vicat softening temperature EN ISO 306
- Shore hardness scale A and D, according to EN ISO 868
- Rockwell ball indentation hardness test according to EN ISO 2039
- Melt Mass-Flow Rate (MFR) according to EN ISO 1133
- Differential scanning calorimetry (DSC)
- Thermogravimetric analysis (TGA)
- Dynamic mechanical thermal analysis (DMTA)
Head
Piotr Jankowski, PhD Sc. Eng.
phone +48 453 056 197
piotr.jankowski@ichp.lukasiewicz.gov.pl
Research topics
- Research into the flame retardancy of plastics (polyethylene, polypropylene, polyurethanes, polyesters, epoxies, polystyrene and others).
- Synthesis and modification of halogen-free flame retardants, including Intumescent Flame Retardant System (IFRs), synthesis of flame retardants based on epoxy resin technology.
- Selection of flame retardants that work effectively in a composition with a given plastic.
- Technologies for obtaining polyester resins, epoxy resins – including resins with special properties, liquid, low-melt, solid epoxy resins, elasticising agents for epoxy resins.
- Technologies for obtaining composites including nanocomposites based on duroplastics.
- Synthesis of auxiliaries for selected engineering resins – including plasticisers derived from by-products and waste products
- Technologies for urea, melamine, phenol-formaldehyde resins – including melamine foams and formaldehyde-reduced resins.
- Technologies for polyurethane plastics – new types of insulation materials (modular construction), flexible polyurethane foams.
- Waterborne polyester resin technologies.
- New polymeric materials: chemical and physico-chemical modification of thermo- and duroplastics.
- New polymeric materials: functional polymers with the addition of structure modifiers or functionalized hybrid natural or waste fillers.
- Thermoplastic, solvent-free hot-melt adhesives: polycondensation adhesives (polyamide, polyester), adhesives based on PP, PE, EVA copolymers, APAO and block rubbers (SIS, SBS, SEBS) and others, adhesives used in the following industries: leather, electrical engineering, construction, furniture, packaging and electronics.453 056 197
- Polymer superabsorbent technologies (SAPs).
- Natural products in polymer technologies, biodegradable polymers.
- Optimization of existing technologies related to the above.
Head
Katarzyna Łęczycka-Wilk, PhD. Sc.
phone +48 453 056 203
katarzyna.leczycka-wilk@ichp.lukasiewicz.gov.pl
Research topics
- Design of new biopolymers with competitive antimicrobial, antifungal and antioxidant properties
- Modification of the physicochemical and functional properties of biodegradable natural polymers (especially chitosan) with potential application in the packaging industry
- Preparation of new plasticisers for polymeric materials based on polysaccharides, including the synthesis of deep eutectic solvents
- Edible coatings and active packaging based on polymers of natural origin as competition for contemporary packaging materials used in the food industry
- Investigation into the release of active ingredients from polymer matrices
- Preparation and physicochemical characterisation of new crosslinking agents and polymer blends and composites
- Chemical and physical crosslinking of polymer blends
- Emulsion, suspension and block polymerisation – preparation of polymer suspensions and monodisperse latexes and transparent plastics
- Purification and separation of substances (e.g. from plant material) by extraction and by sorption and desorption on ionic or non-ionic resins
- Preparation of organic fungicides and bactericides and natural fertilisers
Head
Jarosław Przybylski, PhD. Sc. Eng.
phone +48 453 056 213
jaroslaw.przybylski@ichp.lukasiewicz.gov.pl
Research topics
- Synthesis of polyurethanes and silicone-urethanes cross-linking with atmospheric moisture,
- Aqueous dispersions of polyurethanes, silicone-urethanes, acrylic-urethanes, silicone-acrylics, acrylic-alkyds, especially in application as coating materials,
- Isocyanate modification of asphaltenes, coal tar pitch and hydrocarbon resins,
- Association of polyurethane thickeners,
- Aging and application testing of adhesives, coatings, putties and compositions,
- Polymeric plasticisers for PVC,
- Solvent-free and water-dispersible binders for UV-crosslinking coatings,
- Silicone-urethanes as:
- living cell scaffolds,
- solid polymer electrolytes,
- membranes for the separation of liquid and gaseous mixtures,
- Polymer nanopowders as impact modifiers for powder coatings and polymer plastics,
- Coating materials for special applications, e.g. self-healing polymeric coatings, electromagnetic radiation shielding, etc,
- Reticulated glassy carbon,
- Polymeric consumables used in 3D printers.
- Studies of selected properties of coating materials (paints and varnishes).
Head
Marcin Kumosiński, M. Sc. Eng.
phone +48 453 056 210
marcin.kumosinski@ichp.lukasiewicz.gov.pl
Research topics
STAGE I: Research work in the polymerisation of vinyl chloride (PVC synthesis)
→ Development of new reaction formulation compositions to improve the quality of the resulting polyvinyl chloride
→ Optimisation of PVC synthesis processes towards: increasing yields, formulation compositions
→ Research to develop PVC types for new applications
→ Investigation of the influence of the individual components of the reaction mixture on the properties of PVC
→ Investigation of new auxiliary substances in the PVC synthesis process and determination of their influence on the quality of the PVC obtained
→ Investigation of environmental requirements of the PVC synthesis process.
STAGE II: Research work in the preparation of dry mix (dry-blend)
→ Development of a dry mix recipe that meets specific processing properties
→ Development of a dry mix recipe that meets specific processing properties
→ Modification of the recipe for optimization: composition, properties, price
→ Study of the effectiveness of new processing agents and determination of their method of use (quantity, stage of introduction into the mixture) on the properties of the finished product and the processing process
→ Qualitative studies of PVC blends.
STAGE III: Processing studies
→ Gelation time
→ Dynamic stability
→ Determination of processing temperature of powders as well as plastic granulates
→ Performing viscosity measurements
→ Performance of kinematic viscosity using a capillary nozzle
→ Extrudability tests
→ Analysis of test results and correlations with reference samples
→ Execution of granular sample of the tested mixture (dry blend).
The research facilities include:
→ MetaStation 4E – Torque rheometer with software and Internet connection
→ Conical twin-screw extruder – counter-rotating CTSE
→ Vertical auger dispenser
→ Extrusion heads:
– slotted, flexlip type. Nozzle dimensions: 50 x 0.05 to 2.0 mm
– Rod head with 2 ¾” threaded ring, and interchangeable nozzles: Ø 3.0 mm, Ø 4.0 mm, Ø 5.0 mm
→ Planetary mixer P 600
→ Measuring rotor 50 EHT
→ Transport tape
→ Cooling bath
→ Granulator
→ Brabender-MetaBridge software for data correlation